Advancing miniaturization results in the fact that the vast majority of components used in the currently manufactured electronics are of surface mounted type. Their small dimensions, flat enclosures allow, on the one hand, for the miniaturization of the systems being manufactured and, on the other hand, for faster production thanks to the development of SMT machines: printers applying solder paste and Pick&Place devices.
Despite the above, the current level of technology does not allow the design of all electronics based solely on surface mount technology. All the time we need power connectors, large capacitors or power transistors, which due to their size or current values cannot be soldered in this way. For these components it is necessary to use the older technology — the THT assembly. In the standard production process, the soldering of the THT components is done on the so-called wave due to the very high performance of these machines, but it also has its price.
The wave soldering process requires complex carriers made of very expensive materials. The carriers must also be made individually for each application that will be subjected to the wave soldering process. Adding to this the significant cost of electricity needed to melt the entire crucible of the binder, this process is only cost-effective for large and very large batches of products.
Due to increasing miniaturization, there is also a selective soldering process, in which the leads of components assembled using the THT technology are set on a narrow nozzle with a solder, so that only places of interest are soldered, unfortunately, this process is much slower and much more complicated than wave soldering. There is, of course, also the possibility of manual soldering of THT components, which may be cost-effective for small batches of products, but with increasing labour costs it is not cost-effective for large-scale production.
REECO SOLDERING ROBOT
An alternative to these standard processes, has been recently brought about by the rapid advances in robotics and automation.
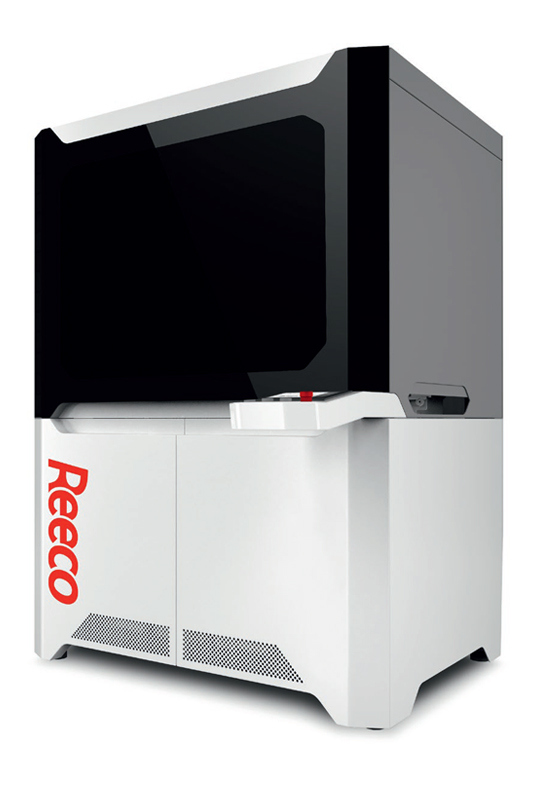
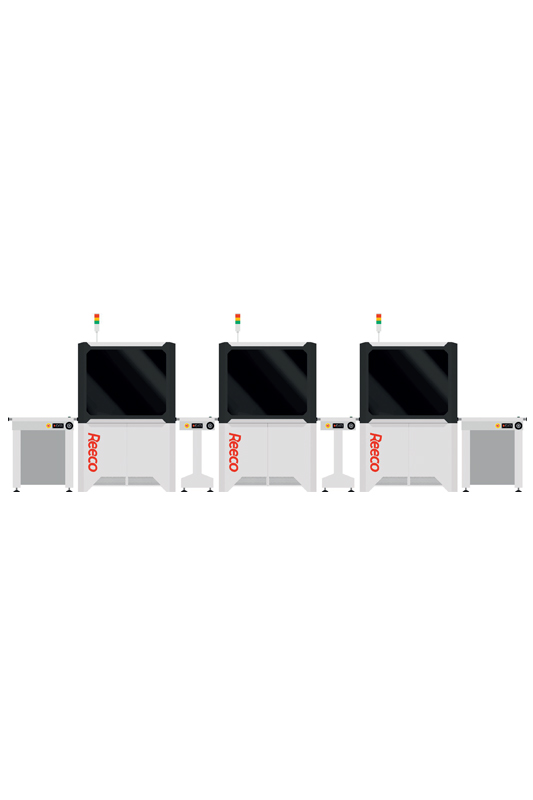
More and more affordable devices are being implemented in almost all industries. The REECO soldering robot, developed by the RENEX Group, is part of this trend. It was designed for medium-volume production in THT technology — unprofitable for the reasons mentioned above — using both wave soldering and hand soldering. A unique feature of the REECO Soldering Robot is its full capacity to work in the production line. Two or more robots can form cooperative assemblies, e.g. when the process requires the use of several types of tips, or can work with other equipment and loader and unloader stations.
The used PLC system controls all auxiliary equipment such as transport, soldering generator, wire feeder, tip cleaning station and presents the current status of the machine both on the 7-inch operating panel and via the signal tower. The robot eliminates the need for expensive carriers used in the wave process.
ROBOT IN ACTION
We present an interview with Andrzej Szymański, the owner of LARS — a world-renowned Polish company in the electronics industry that produces the highest quality lighting.
What problems or needs made you look for solutions in the field of automation of THT production processes? We have a contract with a foreign customer, where in the production process we have to solder 5 wire-wire-through connectors at an angle of 8.5°. Of course we made the right instruments, but making tens of thousands of solders by hand did not guarantee repeatability and therefore quality.
What factors made you choose the solution offered by the REECO soldering robot? We were looking for an automated solution that would ensure repeatability, eliminate human errors and, additionally, would not generate flux fumes at assembly stations. As RENEX is well known to us (they were already a supplier of machines for us) and we have the best possible experience in service and maintenance, we decided to address an inquiry to RENEX. It turned out that they have just developed their own solution at a competitive price compared to foreign offers.
What were the results of implementing the solution in the form of the REECO soldering robot? We have achieved the results, the whole process for the above mentioned contractor is realized with the RENEX robot, we do not have any quality complaints in this process.
Has the implementation of the solution in the form of the REECO soldering robot translated into increased production efficiency? The process of soldering using the robot is not much faster than manual soldering (the same must be done to heat up the elements and apply the solder), but it is undoubtedly more accurate and highly repeatable. Nevertheless, it certainly replaces at least one person, which is extremely important from the point of view of the current labour market, where it is difficult to find qualified workers.
Is any of the functionality of the robot particularly important/helpful for you? The accuracy of the edge conveyor is very important, so that the tip always hits the exact spot you want. During use, programming the robot has proven to be a little bit unergonomic. It required the manual disconnecting of the RS-232 connector plug, between programming and production modes. The solution was to install an additional switch, which the manufacturer easily agreed to without losing warranty rights, and promised to look at the problem and make it easier for future products.
We had one of the first robots to be manufactured by RENEX, so we considered it a minor inconvenience that could be easily removed.
Do you have further plans to develop and cooperate with the RENEX Group in the field of REECO soldering robots (e.g. line development) or other devices from the company’s range? We are not only planning, but are already in talks about buying a few more machines to complement our current lines and increase our production capacity.
MAN VS ROBOT
The performance of the soldering robot is well illustrated by the last series of Man vs Robot duels. As part of the «Polish Soldering Championship» — RSC 2019, Warsaw Industry Week and Productronica in Munich the REECO soldering robot faced, among others, European Champion 2017 and champions from Poland, China, Great Britain and Germany. The task was to create 256 soldering connections. For masters working within the boundaries of human hands this task takes from about 4 to about 7 minutes. The REECO soldering robot performs this task in just over 5 minutes. This example shows how huge progress in automation has been and continues to be made in recent years. The speed of work that is only achievable by the best soldering engineers in the world, and only for a short period of time, can be realized by the robot practically 24 hours a day — without a break. The REECO soldering robot is part of the REECO family of robots ready to use modular solutions for a wide range of industries. Other models allow automation of processes (production stages) such as labelling, screw assembly, dispensing and much more.
All those interested are welcome to visit the RENEX Technology Centre and the Demoroom where it is possible to get acquainted with REECO soldering robots and to contact RENEX technical and commercial advisors.