Investments in advanced technologies are crucial for the development of an enterprise. However, fully utilizing their potential is only possible through adequate skills and knowledge, highlighting the importance of solid equipment operation training.
When a company decides to purchase new equipment, it expects efficiency, reliability, and full utilization of its potential. These aspects are key to increasing productivity and efficiency, saving time and resources. However, sometimes there is a problem that prevents these benefits from being achieved – improper or incomplete use of the equipment after purchase.
Problems Arising from Lack of Skills in Operating Modern Equipment
In a rapidly developing technological world, companies invest significant resources in acquiring the latest equipment, such as production machines, soldering devices, or industrial furniture. Many of them, striving to achieve higher efficiency and competitiveness, use innovative technological solutions. However, after acquiring advanced equipment, it often happens that teams are unable to fully utilize its capabilities, usually due to a lack of appropriate skills or insufficient knowledge about operating the newly purchased devices.
Such situations can lead to many negative consequences. Firstly, improper use of the equipment can result not only in financial losses due to not fully utilizing the investment’s potential but also in a decrease in work efficiency and productivity. Secondly, it can increase the risk of device failure, which involves additional service costs. Additionally, it can lead to employee frustration, as they may feel overwhelmed by the difficulties associated with operating complex equipment. Consequently, this can lead to decreased job satisfaction and lowered team morale.
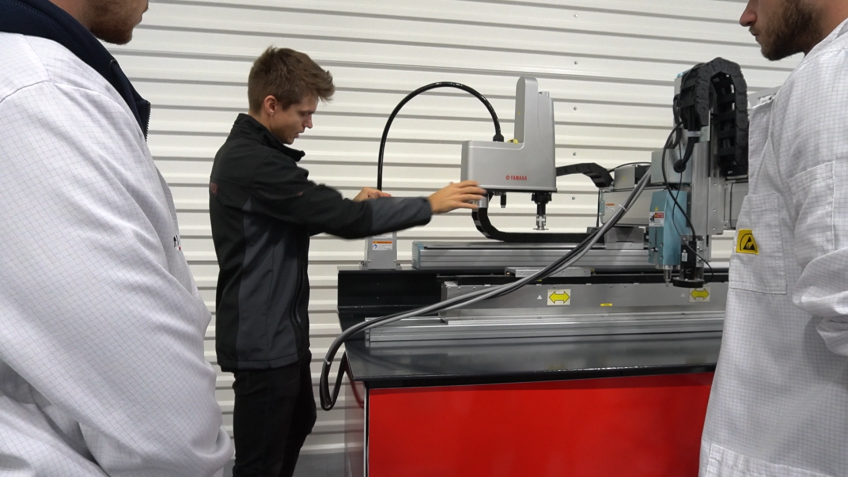
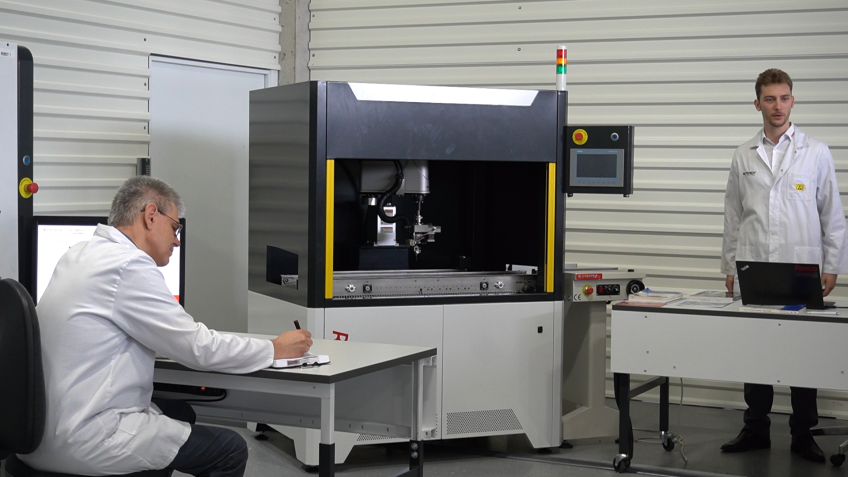
Equipment Operation Training – The Key to Efficiency
To counteract problems related to improper operation of modern devices, investing in education and training for staff is crucial. These are key elements of a strategy to optimize the use of purchased equipment. Equipment operation training is an investment that brings numerous benefits. First and foremost, it enables employees to acquire the knowledge and skills necessary for effective work with new devices, translating into full utilization of these tools’ potential.
Effective training allows understanding the specifics of equipment operation, which directly translates into increased productivity and work efficiency. Employees who are aware of the device’s capabilities and functions can better adapt their actions to the technological possibilities, leading to higher quality results. Additionally, proper training minimizes the risk of errors in equipment operation, which can lead to costly failures or unnecessary wear of the device. Reducing misunderstandings and mistakes significantly lowers costs associated with improper equipment use.
Finally, well-conducted equipment operation training can significantly boost team morale. Employees who feel confident and competent in handling devices are motivated and satisfied with their work, creating a positive work atmosphere and better company results.
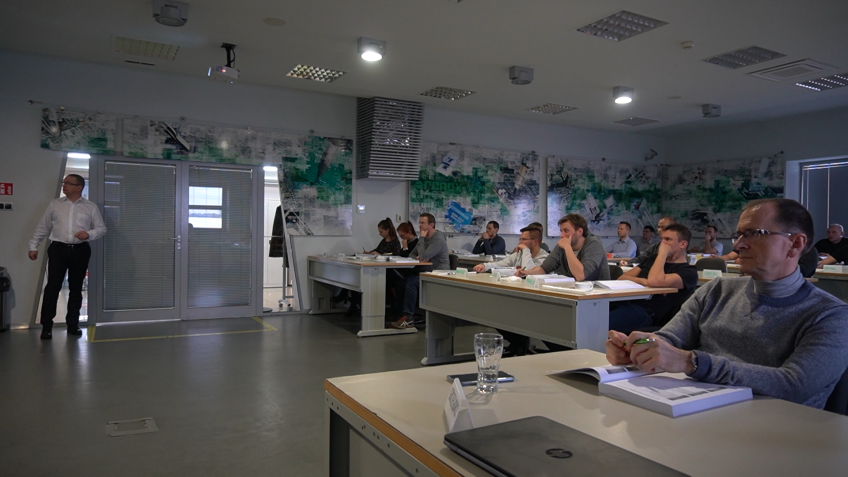
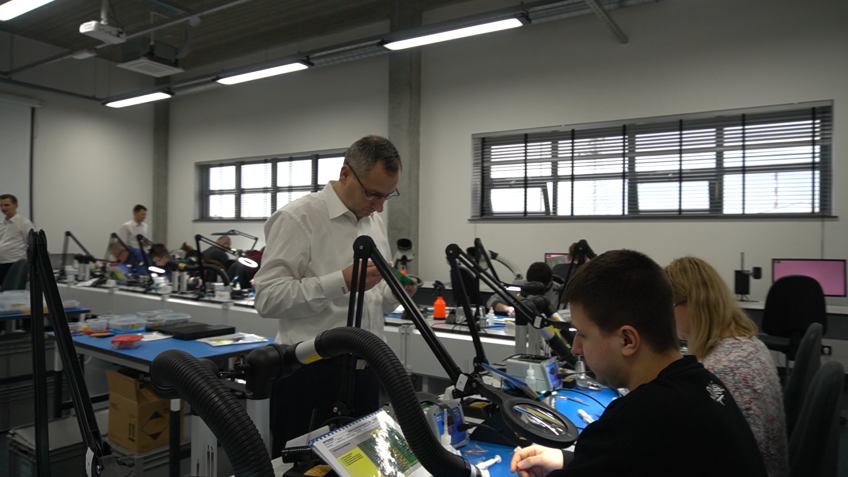
RENEX Group – Specialists in Equipment Operation Training
RENEX Group, a leading provider of comprehensive solutions for the electronics industry, understands how crucial skills and knowledge are in operating purchased devices. The company offers a range of specialized equipment operation training, ensuring that investments in modern technologies translate into real, measurable benefits. Thus, RENEX Group not only supplies modern equipment for the electronics industry but also emphasizes the importance of proficient equipment operation by its clients.
Training conducted by RENEX Group’s Technical and Sales Advisors focuses on the practical use of the device’s functions. The combination of commercial experience with technical know-how makes them extremely useful for any company wanting to fully exploit the potential of its investment.
The goal of the training is to ensure that every client who decides to purchase equipment from RENEX Group receives not only a high-quality device but also knowledge on how to operate it. Investment in technology then becomes a real, measurable benefit for the company.
What distinguishes RENEX Group’s training offer are the courses conducted at the Technology and Training Center.
Participants have the opportunity to gain valuable skills, knowledge, and prestigious certificates confirming their competencies under the supervision of experienced trainers. The Center’s infrastructure includes complete electronics production lines, including solder paste printers, Pick & Place machines, and AOI systems from YAMAHA, REECO industrial robots, wave soldering machines, SEC X-ray inspection devices, reworking devices, and universal industrial robots from YAMAHA. Training sessions cover both theory and practice, providing best industry practices and valuable tips.
All these training sessions are designed with practical application in mind. Participants have the chance to test their skills and acquired knowledge in a real environment, contributing to a better understanding of the material and enabling the rapid implementation of new skills in daily tasks.
In the era of rapid technological development, managing them can be challenging. That is why RENEX Group, through comprehensive training, gives companies the opportunity to fully utilize the potential of their investments, while increasing their competitiveness in the market. This comprehensive approach demonstrates RENEX Group’s full commitment to the success of its clients – the company not only sells equipment but also provides clients with the tools for its effective use.